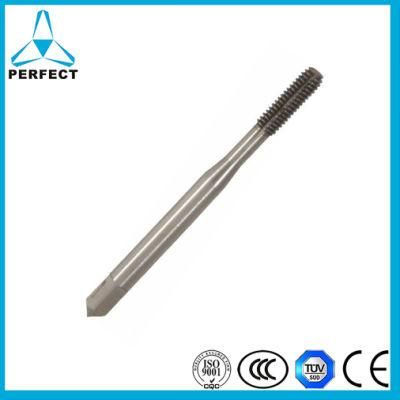
Bright Finished HSS Bottoming Chamfer Thread Forming Sti Taps
Xuzhou Perfect Industry Technology Co., Limited- Type of Tap:Extrusion Tap
- Type of Die:Round Die
- Material:High-speed Steel
- Standard:Metric, British, American
- Application for Machine Tool:Punch
- Application:Motorize, for Steel, Aluminium, Copper, Stainless Steel..
Base Info
- Model NO.:PFT031
- Customized:Non-Customized
- Place of Origin:Jiangsu, China (Mainland)
- Brand Name:Perfect
- Type:Machine Taps
- Raw Material:HSS, M2, M35, Hsse, Cpm
- Surface Treatment:Bright Finish (Tin-Coated, Other High Performanc
- Unit Packing:Plastic Box
- Transport Package:Plastic Box +Inner Box+Carton
- Specification:According to Requirement
- Trademark:Perfect
- Origin:Jiangsu China
- HS Code:8207400000
- Production Capacity:10000 PCS,Per Day
Description
Basic Info.
Model NO. PFT031 Customized Non-Customized Place of Origin Jiangsu, China (Mainland) Brand Name Perfect Type Machine Taps Raw Material HSS, M2, M35, Hsse, Cpm Surface Treatment Bright Finish (Tin-Coated, Other High Performanc Unit Packing Plastic Box Transport Package Plastic Box +Inner Box+Carton Specification According to Requirement Trademark Perfect Origin Jiangsu China HS Code 8207400000 Production Capacity 10000 PCS/Per DayProduct Description
STI TAPSAn STI tap thread tap is designed to create an oversized thread to accommodate the required Heli-Coil insert. Screw Thread Inserts (STI) are helically formed diamond shaped stainless steel or phosphorous bronze wire that screw into a threaded hole to form a mating internal thread. Screw thread inserts are a convenient way of repairing stripped out threads and are also used to provide stronger threads in softer materials than can be obtained by directly tapping the base metal.
Thread Forming Taps for STI Tapped Holes
We receive many inquiries regarding the usage of thread forming taps vs. thread cutting taps for producing STI (screw thread insert) tapped holes. In general, thread forming taps are not recommended by KFS or our competitors for tapping STI holes because of the problems associated with controlling the size and the shape of the resulting minor diameter.
Since thread forming taps are commonly and successfully used in the machining industry, we thought that our readers would benefit from an overview of this product, its applications, and benefits, but also from an understanding of the possible negative consequences associated with using this type of tap for STI tapping.
Thread forming taps (sometimes called cold forming taps) are designed for cold forming threads in ductile materials. These include aluminum, copper, brass, zinc, low carbon steels, and free machining stainless steels. They displace material rather than cut or remove it. The taps do not have flutes or cutting edges and therefore no chips are produced. Chip free tapping is advantageous as there are no chips to clog the tap allowing it to easily thread to the bottom of blind holes. In addition there are no chips remaining to potentially contaminate mating parts or plating operations. The manufacturers of these taps claim that they achieve longer tap life than thread cutting taps, as well as the fact that they can be run at higher tapping speeds. As with thread cutting taps, countersinking before tapping is a good machining practice to prevent a featheredge or burr on the tapped hole that will affect installation of the insert.
Standard Tapping Advantages | STI Tapping Disadvantages |
---|---|
Chipless Tapping | Uncontrolled Minor Diameter |
Faster Tapping Speeds | Concave Minor Diameter Profile |
Longer Tap Life | Insert Installation Problems |
Full Threading in Blind Holes | Excessive Locking Torque |
STI Tapped Holes
It is very difficult to achieve the desired thread minor diameter with thread forming taps. With thread cutting taps, the drilled hole size is the minor diameter. Thread forming taps require a drilled hole size that's calculated based upon the percentage of full thread desired after tapping. Sometimes this requires reaming, as the desired standard drill sizes are not available, or the required tolerances are not achievable by the looser tolerances associated with drilling. When locking inserts are used, an undersize minor diameter condition can cause the insert locking torque to exceed the allowable maximum per NASM8846.
Another serious problem that can result from thread forming taps is that the crests of the thread at the minor diameter can be formed with a concave profile (see diagram). This can negatively affect insert installation and torque, particularly on the smaller and finer thread sizes. Cross threading of the insert upon installation is common with the concave minor diameter profile.